Introducing our Tapestry Project
September 6, 2019 | Land management | 6 minute read
In partnership with the National Trust Textile Conservation Studio and the Arts Society King’s Lynn, we are undertaking some conservation work on our 18th Century English Soho tapestry, Fête Champêtres. We anticipate the work will be a year-long.
The tapestry was slightly water-damaged by a burst pipe in 2017, which we saw as an opportunity to give it a deep clean and strengthen its warps. Warps are the structural pieces of thread which the silk and cotton threads are woven around to make an image. Strengthening the tapestry comes from resewing the slits on the tapestry; this practice is a part of the original manufacturing process. Slits were deliberate in design work, to create a shadowing effect or to make a stark contrast between two colours.
Traditionally, the warps of a tapestry are horizontal, meaning that the weight of the tapestry hangs on the warp. Over time, the stress can tire the fabric and cause it to sag. By strengthening the vertical slits in the tapestry, the weight is distributed more evenly across the tapestry. Our tapestry has 9 warps per cm, which is very fine indeed, being almost a warp per mm. The more the warps, the finer the detail in the design, and less warps make a coarser-looking tapestry.
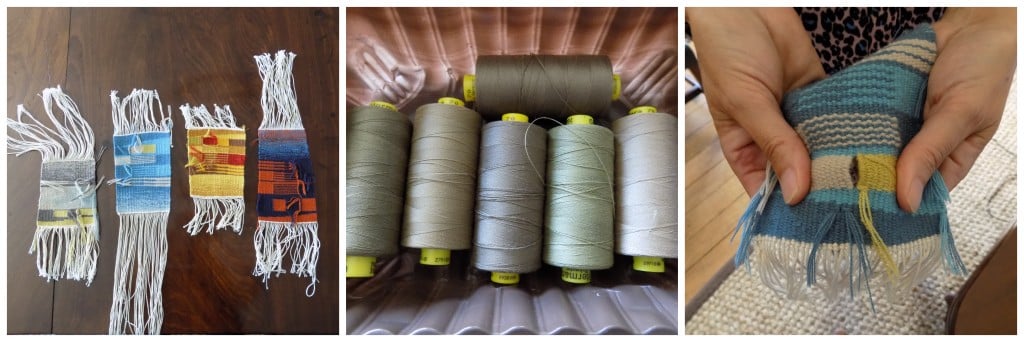
Preparing for the ‘real’ tapestry with examples of stitching techniques and which threads to use.
The National Trust Textile Conservation Studio has worked with us on projects in the past, including netting the State Bedroom coverlet and upholstering various items of furniture. Netting is used on textile items to hold it together and to aid regular cleaning. Aneta Derlak, our housekeeping supervisor and resident needle-worker, is also involved with the project. Aneta is a real asset to Holkham, as she is the first point of call for any sewing that is needed in the Hall. She is looking forward to being involved with this project.
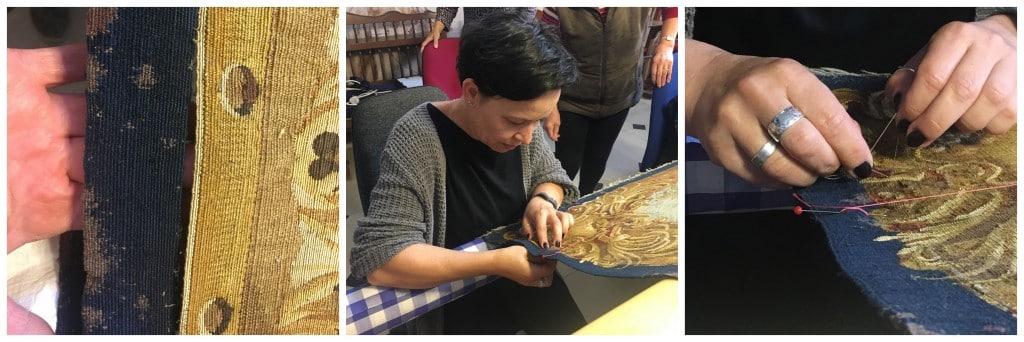
Left: An example of a slit needing to be resewn. Right: Aneta demonstrating her sewing skills.
It is called a Soho tapestry because weavers from disbanded London Tapestry companies went on to create their own tapestries in their own workshops in the area. Weaving tapestries took great skill, and a lot of time; men took seven year apprenticeships to complete their training.
Removing the tapestry from display took a double-platform scaffold, and once off the wall, the hangings, lining and webbing were removed. Before being carefully wrapped up, the tapestry was vacuumed with a special low-suction vacuum cleaner to take off its surface dust. The tapestry was then sent away to the Royal Manufacturers De Wit in Mechelen, Belgium, to be deep-cleaned. Here the tapestry was washed with water and a soft detergent, and brushed with soft brushes before being rinsed thoroughly. Colour testing was run before the water was added to identify the best water:detergent ratio for the textile. T
he tapestry was held down with a special suction machine, and a low-metal bridge was used for conservators to reach the middle of it. After rinsing, it was blotted with specialist towels to remove excess water, then left to dry for 2-3 hours. The entire cleaning process lasted 12 hours. We were thrilled to hear that the tapestry was in really good condition! Rachel Langley, Senior Textile Conservator at the Trust, accompanied the tapestry’s trip to Belgium, to oversee the process. The tidemark from the burst water-pipe was removed, and the colours on the tapestry popped.
Back at Holkham, one of our talented Housemen created a special wooden workbench for the resewing project, out of wood found from across the estate. The team began their first steps last week by sticking Velcro to both a gingham apron and the wooden workbench. The tapestry was then tacked onto the apron, ready to be strengthened. As our team sews, the workbench table will be turned, revealing more of the tapestry to work on.
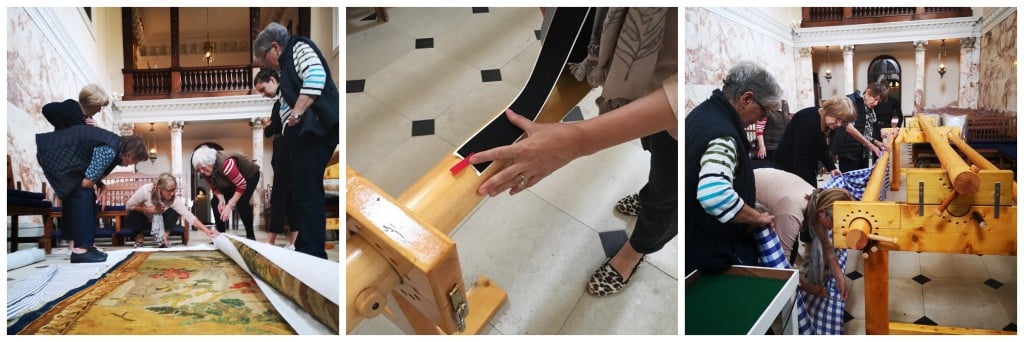
Preparing the workbench for the tapestry.
Yesterday, Rachel Langley conducted a training workshop to teach our team how to resew the slits together, which had loosened over time. She provided one-on-one help and advice to everyone, and our team will now begin the resewing process. We will keep you updated with our progress of this exciting project, through to its re-hanging in the Hall for all to see. The next-step will be lining cotton cambric to the tapestry to protect it from dust and insects. This tapestry is a part of a set, the other tapestry is hanging in the Stranger’s Wing Bathroom, on the visitor route.
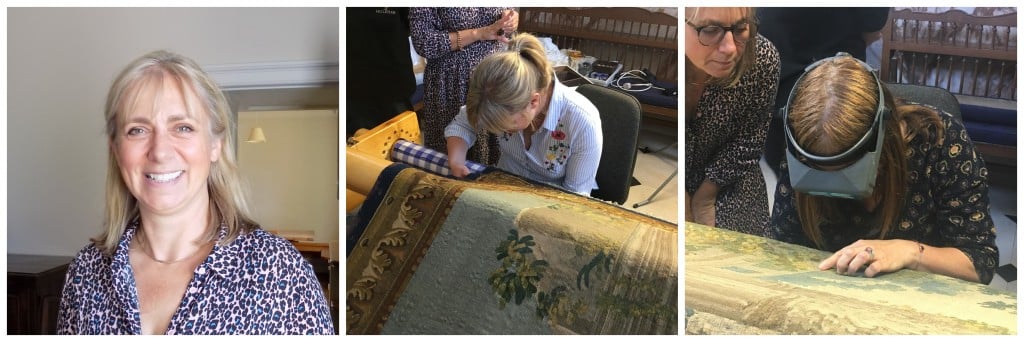
Left: Rachel Langley, Senior Textile Conservator at the National Trust. Right: Resewing the tapestry.
A tapestry is one of the oldest forms of woven textile, and is typically made of silk and wool. Tapestry weaving was highly popular between 1350 and 1800, and came in the form of wall-hangings. They are colourful and often tell stories, with different scenes depicted in a series of tapestries. Older tapestries typically depict stories from the Bible or mythology. Over time, more decorative, domestic scenes were portrayed, often with an oriental influence.
This tapestry was probably woven by Paul Saunders and George Smith Bradshaw. The set depicts le Depart pour Cythère and the Fête Champêtres after designs by Watteau. Figures are dancing and reading in a garden. Together, they are can be interpreted as a description of the joys of love and of how fleeting love can be: Cythera is a Greek island thought to be the birthplace of Venus, goddess of love, and similar depictions of the story show visitors leaving the island, where they had been so happy.
Suzanne, our Head Housekeeper, said “our present conservation work is being added to the tapestry’s history… and ensuring that it will be around for longer.”
View all latest blog posts here.